MAC EDDY CURRENT PRODUCTS
MAC eddy current inspection systems incorporate computer based test instruments and test coils. The test coils interact with the material under test and provide data which is processed and analyzed by the instrument. MAC uses two general types of eddy current test coil technologies: Encircling and Sector Coils, and Spinning or Rotary Probe Coils.ENCIRCLING AND SECTOR EDDY CURRENT COIL TESTERS
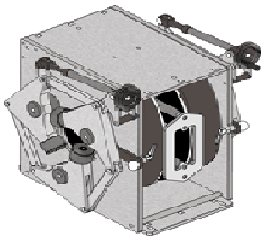
the product under test passes through
or adjacent to an electrical test coil which
has been excited by an alternating current.
This induces a flow of eddy currents around
the test material, or, in the case of a sector coil, in the area under the coil. Short, intermittent anomalies or flaws cause a variation in the eddy current pattern which the instrument detects.
Absolute, differential, or combinations of both coils are available.
Typical applications for encircling/sector eddy current test sensors are:
- Detect short surface and some subsurface defects, on or off-line, in magnetic and non-magnetic wire, bar and tube
- Inspect welded tube for short ID or OD defects in the weld zone or on the full circumference
- Test uniform cross sectional material, including squares, rectangles, hex and round
- Inspect small diameter wire or tube for short defects
- Check continuity and locate welds in single and multi-conductor insulated wire and cable
EDDY CURRENT ROTARY PROBE TESTERS
In rotary probe technology, the product under test moves longitudinally through the rotating test probes resulting in a helical search pattern. As the probe passes over a defect, variations in the induced eddy current pattern are detected. The minimum flaw length which can be consistently detected is a function of the rotary speed of the probe and the throughput speed of the material. Similar results can be obtained by holding the test probe stationary and rotating the material past the probe.- Continuously variable high speed rotaries (1800 6000 RPM)
- Multi-probe headplates to detect shorter defects without sacrificing throughput speed
- Rotary testing is the method of choice for detecting seam type surface defects in non-magnetic and magnetic grades of wire and bar
- Rotary mechanics for up to 7-1/2 inch (191mm) diameter material
- The MultiMac eddy current instrumentation operates with MAC rotaries where long, continuous defects may not be adequately detected by encircling test coils
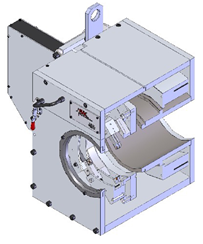
- Detect seam type surface defects in cold drawn wire or cut length bar stock
- Inspect in line with continuous wire operations such as wire drawing, parts forming, re-spooling, or straight and cut
- Inspect cut lengths, usually off-line
- Test parts, such as small shafts and bearings for longitudinal surface defects
MAC Eddy Curret Equipment

MULTIMAC

MINIMAC

PROMAC
Eddy Current Testing is a non-destructive testing (NDT) inspection method used for a variety of purposes, including for flaw detection, material and coating thickness measurements, material identification and establishing the heat treatment condition of certain materials.
BalasHapusEIWAA, Leading NDT Inspection Companies in UAE using both Conventional NDT Inspection technique as well as Advanced NDT Inspection methods. Our Eddy Current Inspection system accompanied by special probes are typically used to obtain higher test sensitivity for non-magnetic conductive materials.Storage tank survey
ADNOC Approved
Welder Qualification Test
Brazing Operator Qualification Test